I've got an animated/moving witch for Halloween that's power supply probably got chewed up by mice in the basement. I could probably get a cable stripper for tiny cables and splice them together, but I would rather just get a brand new cable if not too pricey.
Specs: Class 2 Power Supply AC/DC Adapter - Model: JY15-060-100-UD - Input: 100-240V ~ 50/60Hz 0.4A - Output: 6V - 1000mA (or 1A).
The tip is approx. 5mm wide measured end to end.
Searched for it via Google, Amazon, and eBay with no results for this specific model.
The closest thing I could find was one on eBay that has the right voltage and amperage, but the tip isn't right.
What to do?

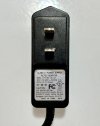
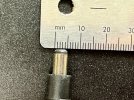
Edit: here's a picture of the witch that was purchased at Spirit Halloween about 12 years ago.
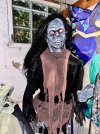
Specs: Class 2 Power Supply AC/DC Adapter - Model: JY15-060-100-UD - Input: 100-240V ~ 50/60Hz 0.4A - Output: 6V - 1000mA (or 1A).
The tip is approx. 5mm wide measured end to end.
Searched for it via Google, Amazon, and eBay with no results for this specific model.
The closest thing I could find was one on eBay that has the right voltage and amperage, but the tip isn't right.
What to do?

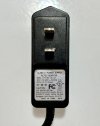
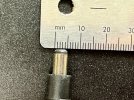
Edit: here's a picture of the witch that was purchased at Spirit Halloween about 12 years ago.
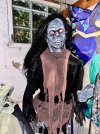
Last edited: